Fréquence
2019
A visual exploration of materials’ former liquid and dynamic state.
A visual exploration of materials’ former liquid and dynamic state.
Our experience of materials and products often conceals the morphing phases through which they went before reaching their final shape. Fréquence is a material exploration aiming at enhancing the tumultuous liquid state that most ceramic and metal items had to undergo before reaching us, and casts a new light on their apparent placidity and stillness.
Case
I was given the opportunity to observe and learn casting techniques both for ceramic and metal. Though very different, these two materials show peculiar similarities when it comes to the way they are processed: a mineral mold of plaster or sand is created that shapes them when liquid and that accompanies their primordial transition towards the solid state. I was inspired to explore the aesthetics of this transition within the shape of the final items.
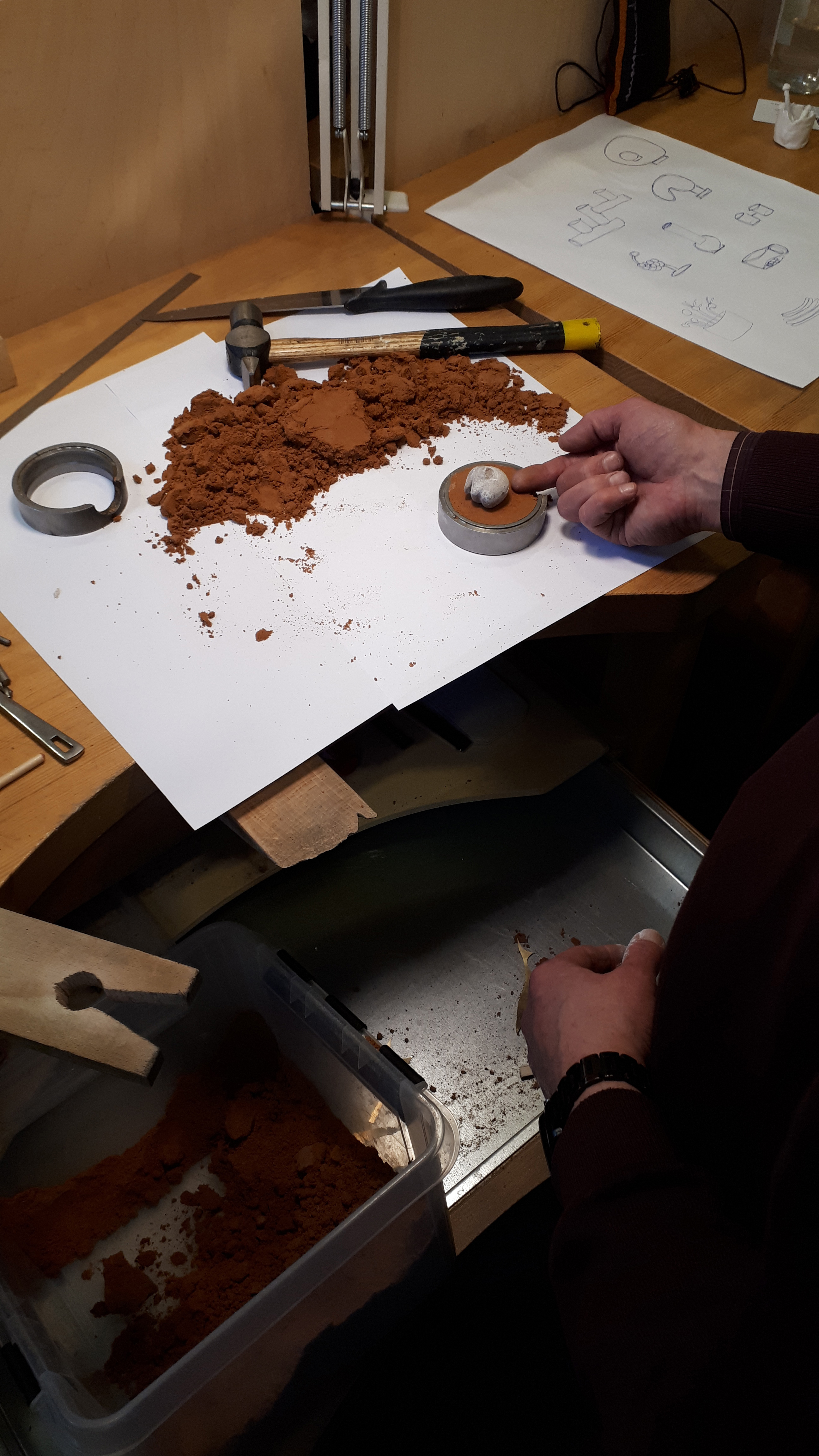
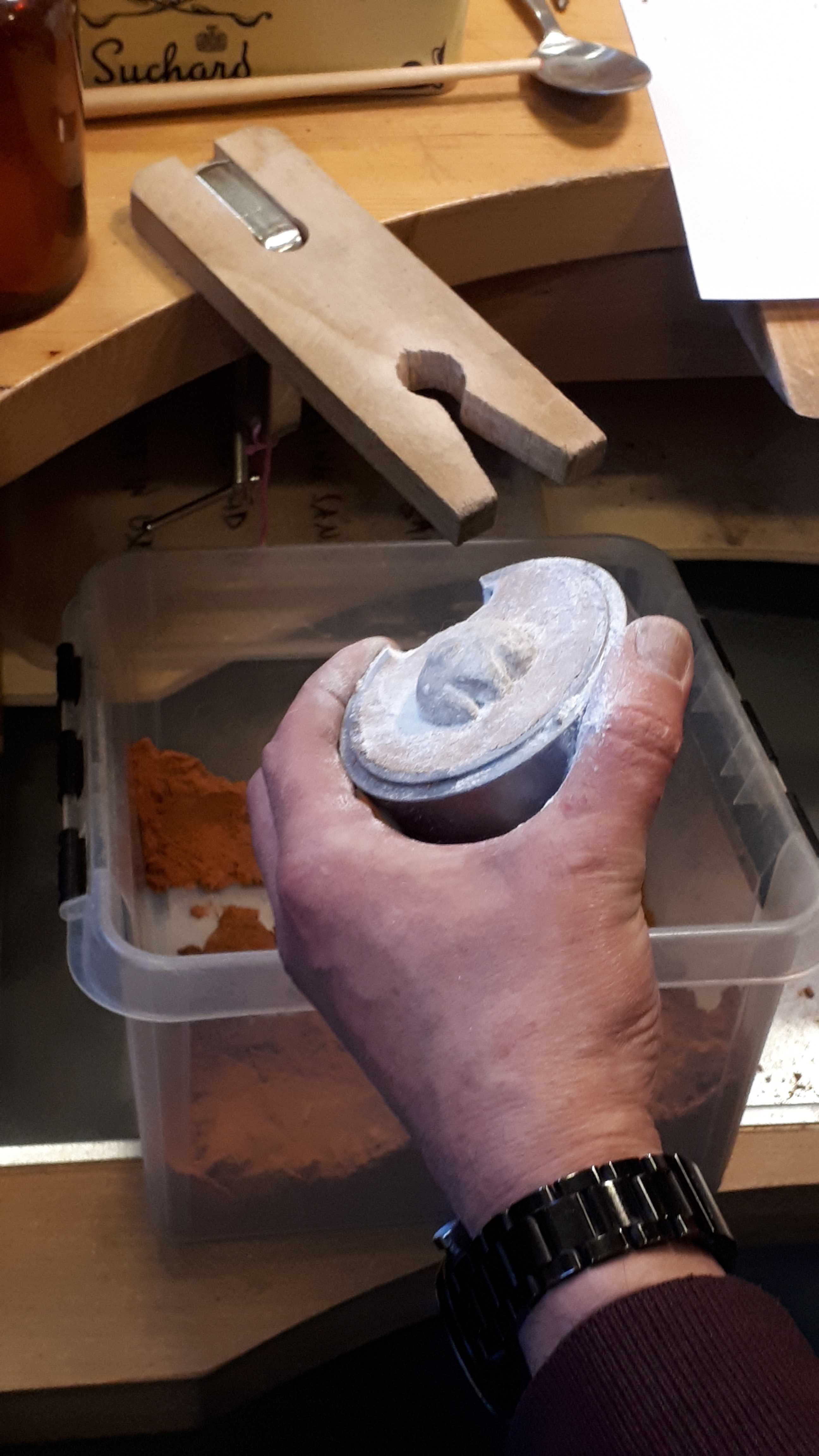
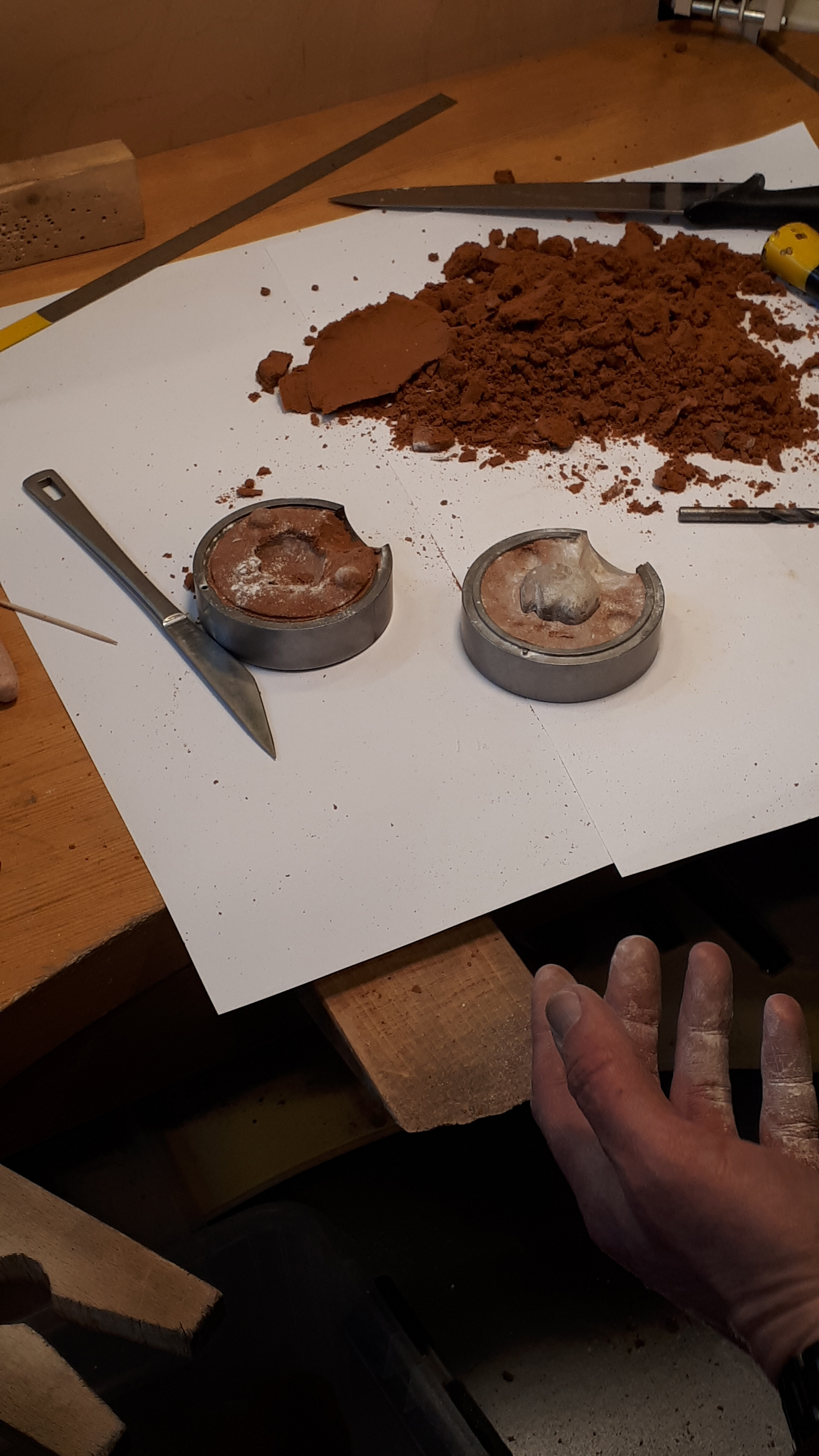
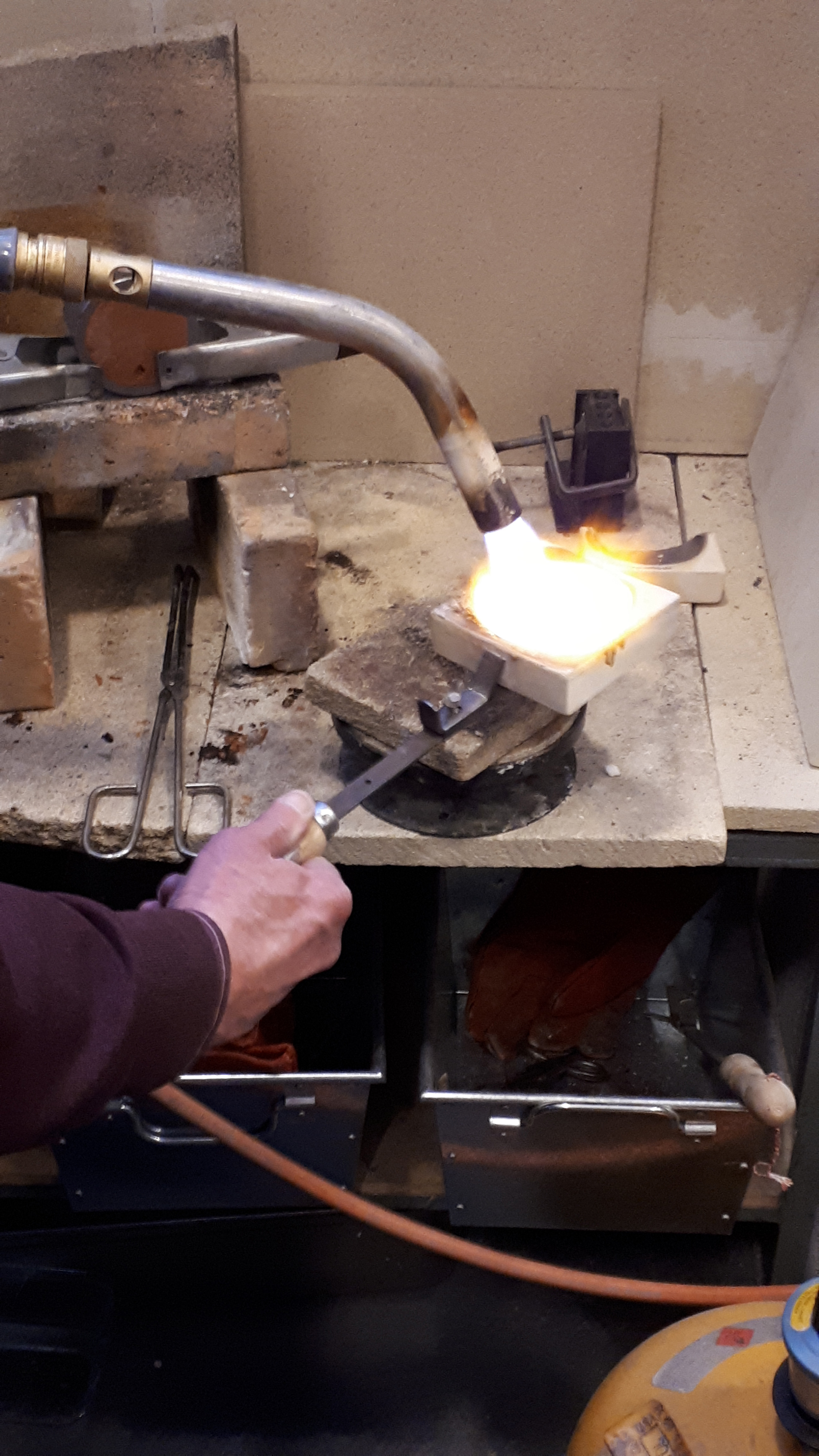




Approach
Having observed, assimilated and experimented with the traditional techniques of mold making and casting, both for ceramic and metal, made me want to push the boundaries of these crafts by connecting them with digital technologies - a recurring pattern in my work. I was convinced that, striving to represent the liquid state of these materials, parametric modelisation would be of great help.
Nevertheless, before experimenting digitally,
I started my exploration with very analogical setups. I recorded the undulations, waves and splashes that occur when liquids interact and drift, setting a visual base to my experiments.
I then moved to the digital sphere and, naively exploring softwares such as Grasshopper and Houdini, developed different representations of moving liquids, from pretty abstract to more formal ones. I also experimented, at this occasion, various visual languages to communicate the project.
I started my exploration with very analogical setups. I recorded the undulations, waves and splashes that occur when liquids interact and drift, setting a visual base to my experiments.
I then moved to the digital sphere and, naively exploring softwares such as Grasshopper and Houdini, developed different representations of moving liquids, from pretty abstract to more formal ones. I also experimented, at this occasion, various visual languages to communicate the project.
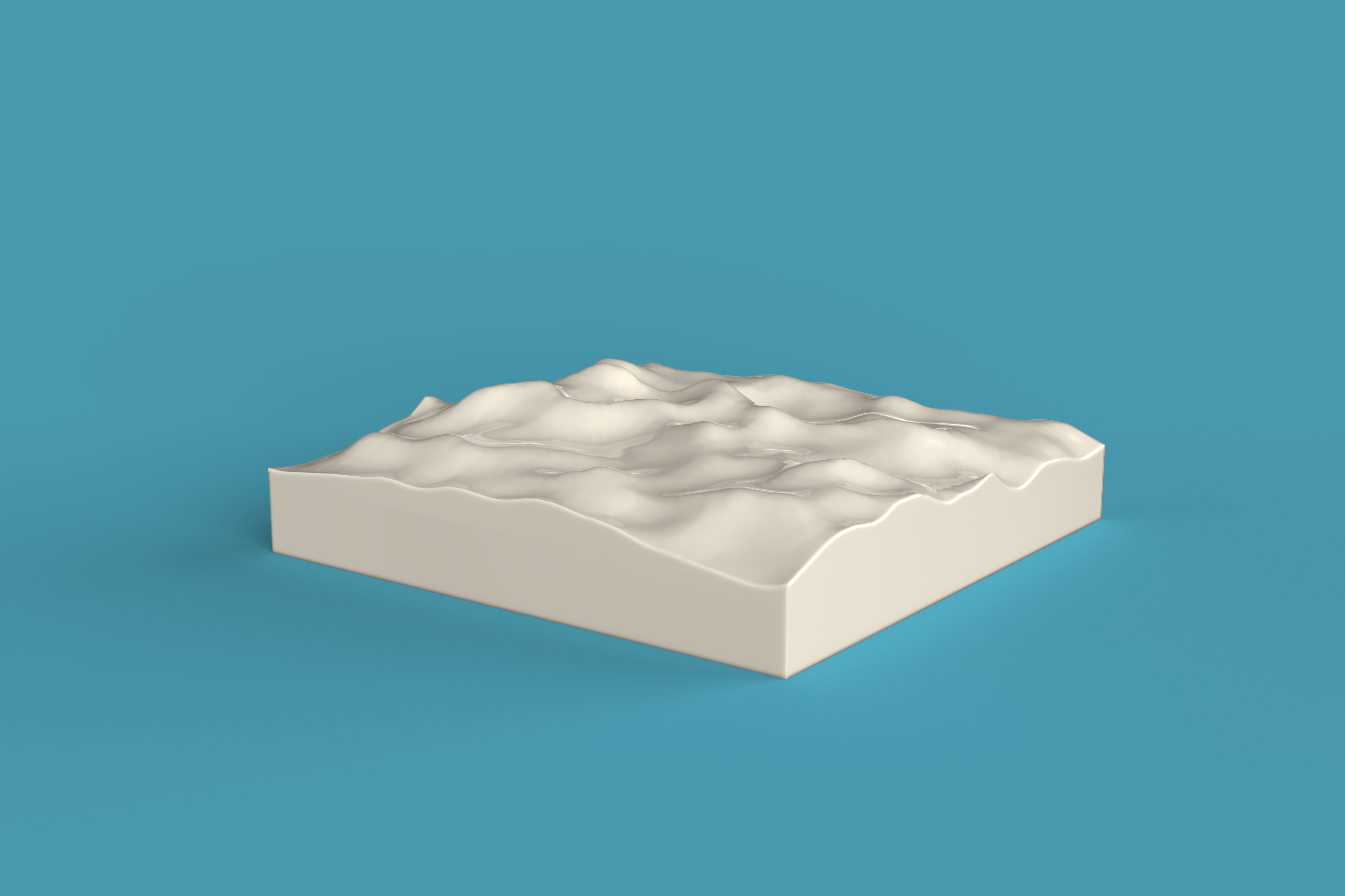
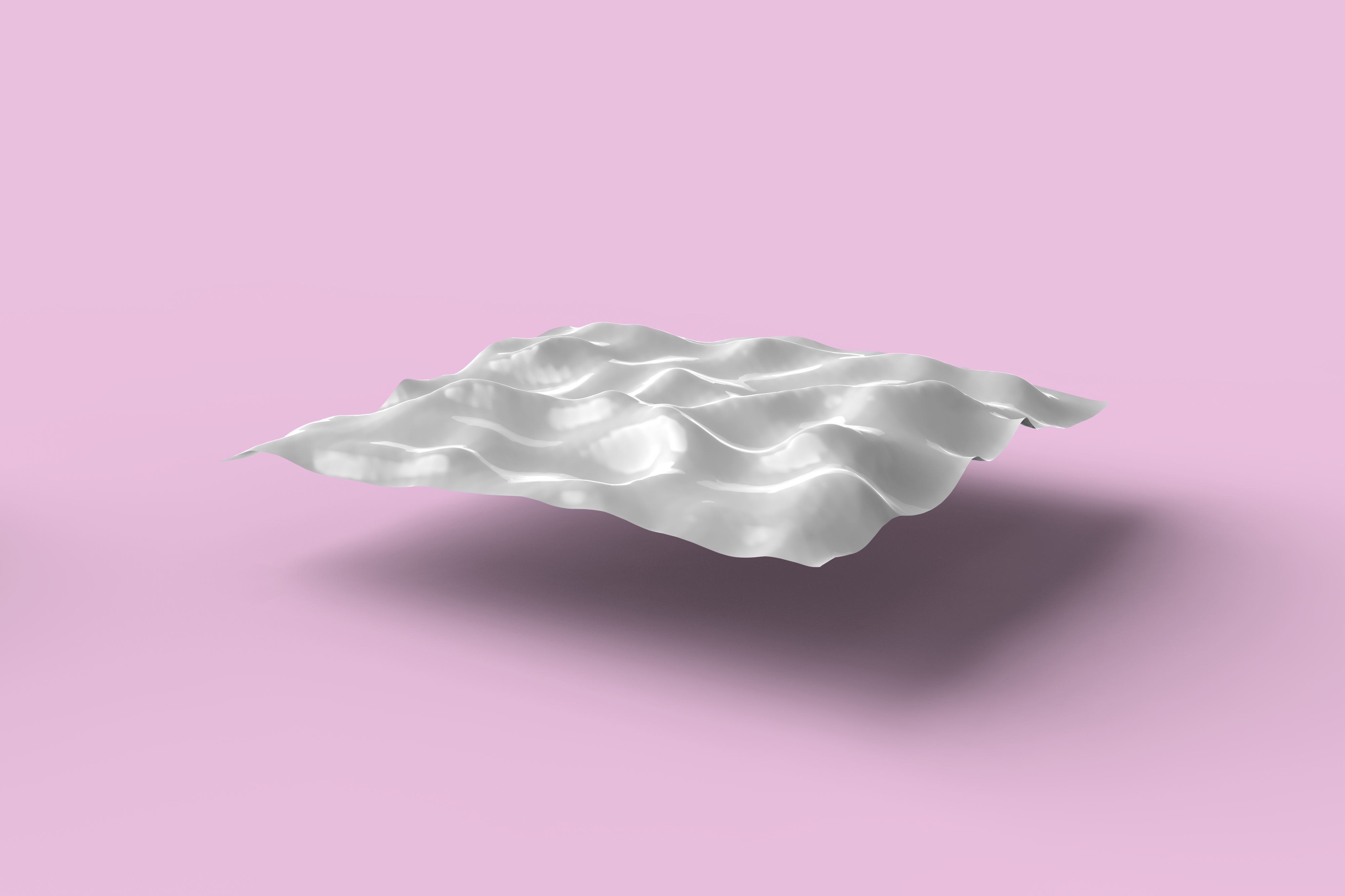
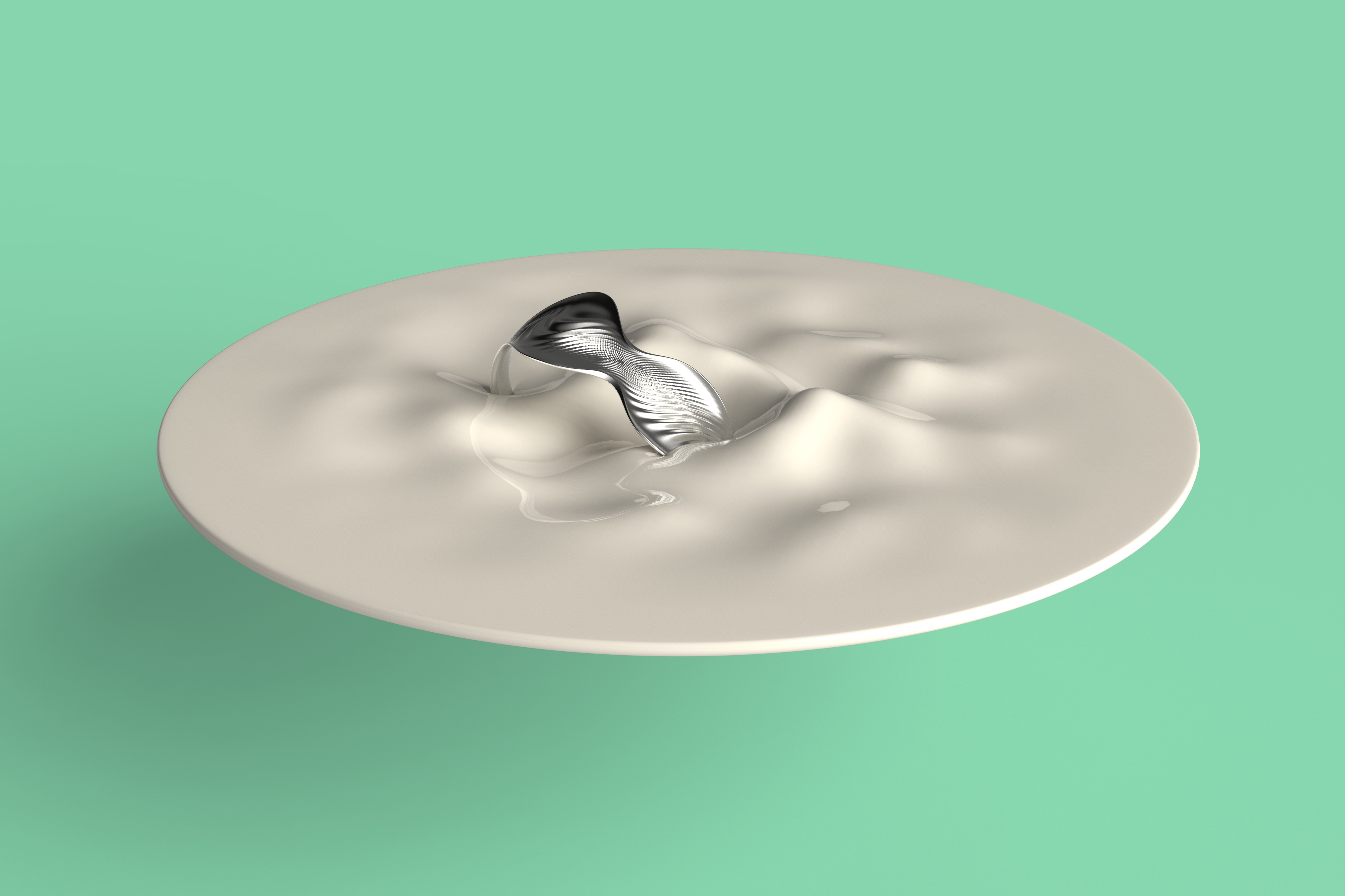
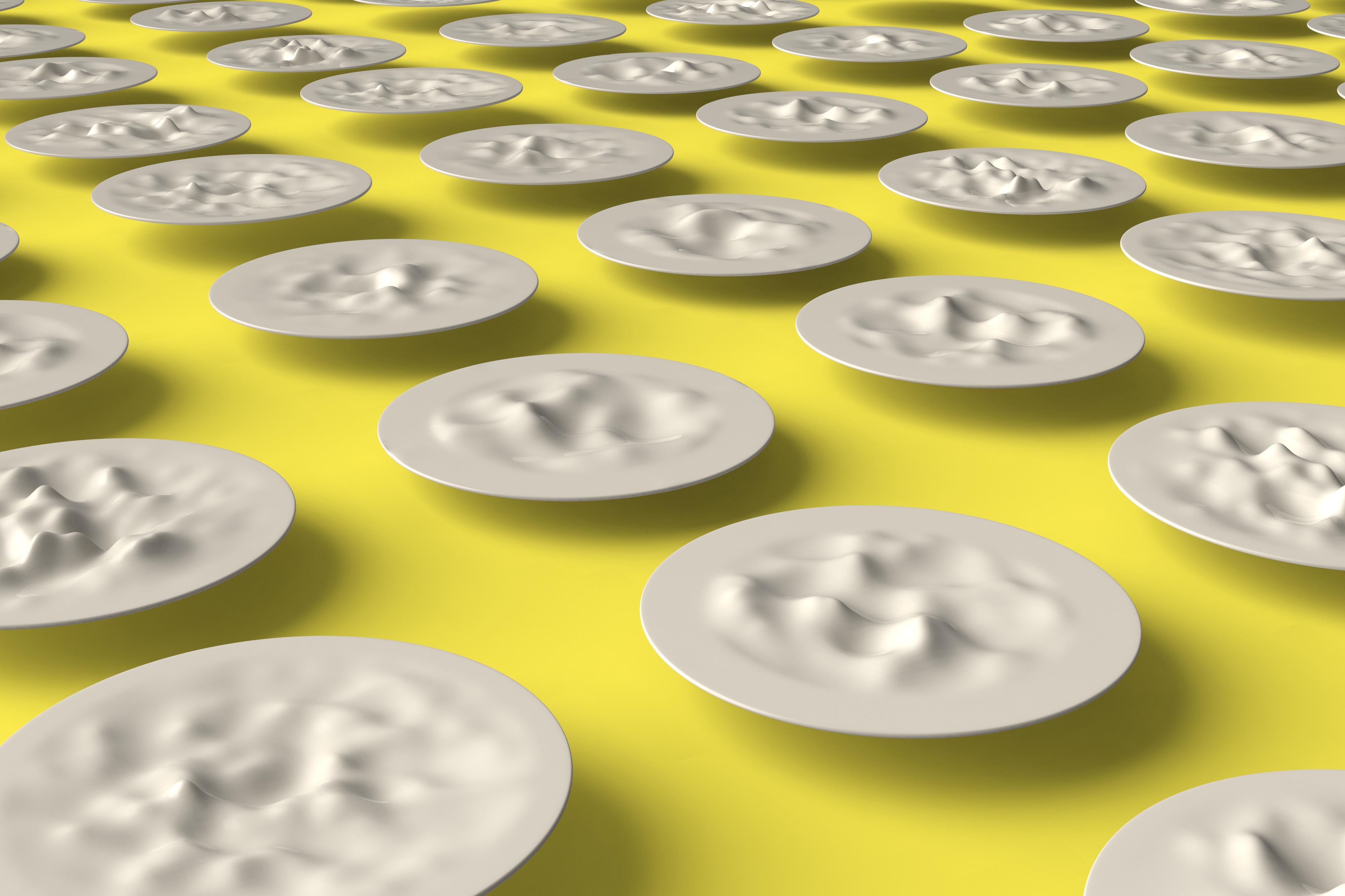
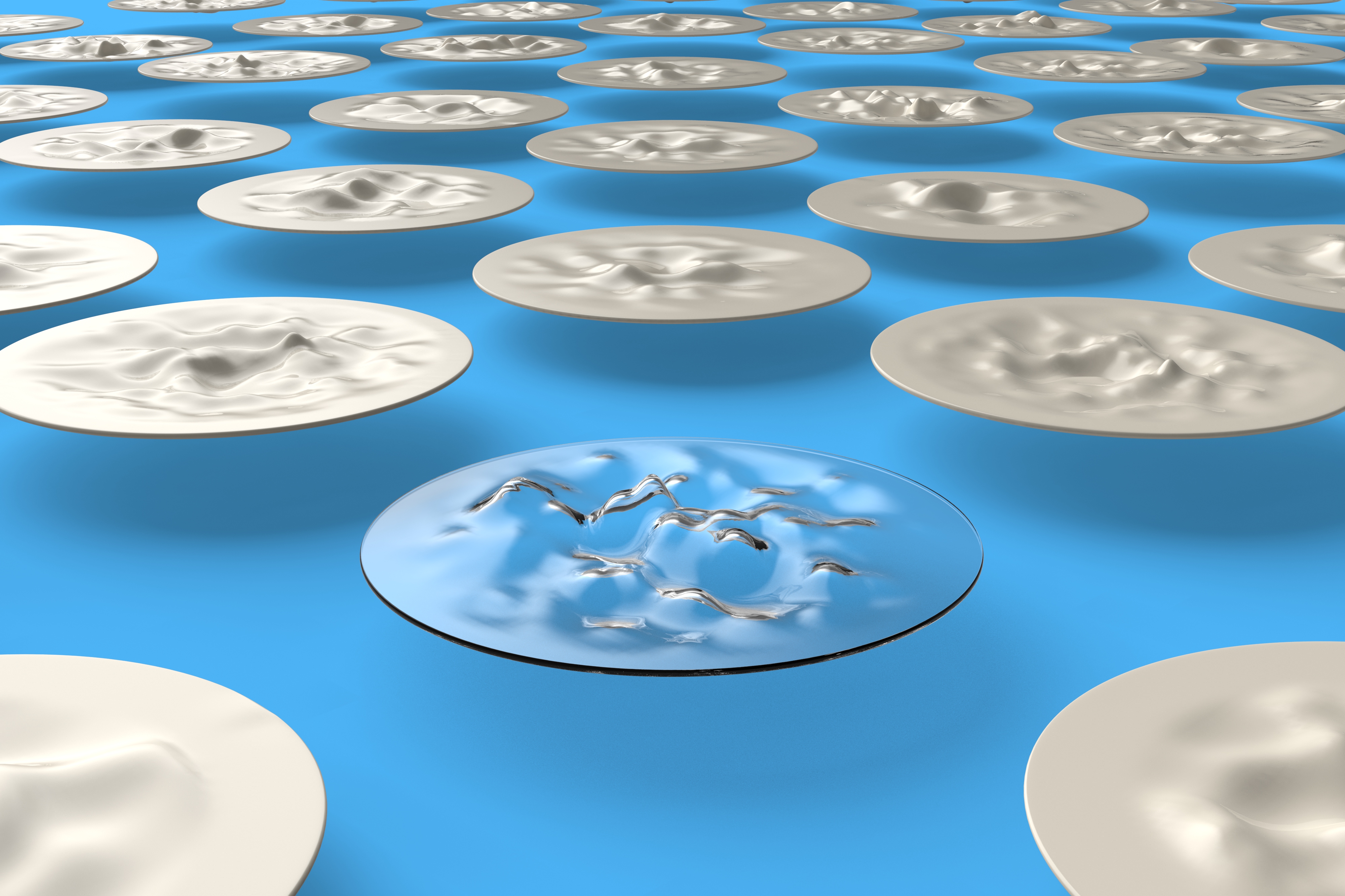
In order to best showcase the outcomes of this formal inquiry, I decided to turn it into a collection of jewels and displays, using metal and ceramic in complementary roles. I used 3D printing to generate shapes that I used in making plaster molds, themself used to cast the ceramic surfaces. 3D printing was also at the core of the metal process, since I printed the jewels in a castable resin which served as the base of the mold making and silver-casting processes.
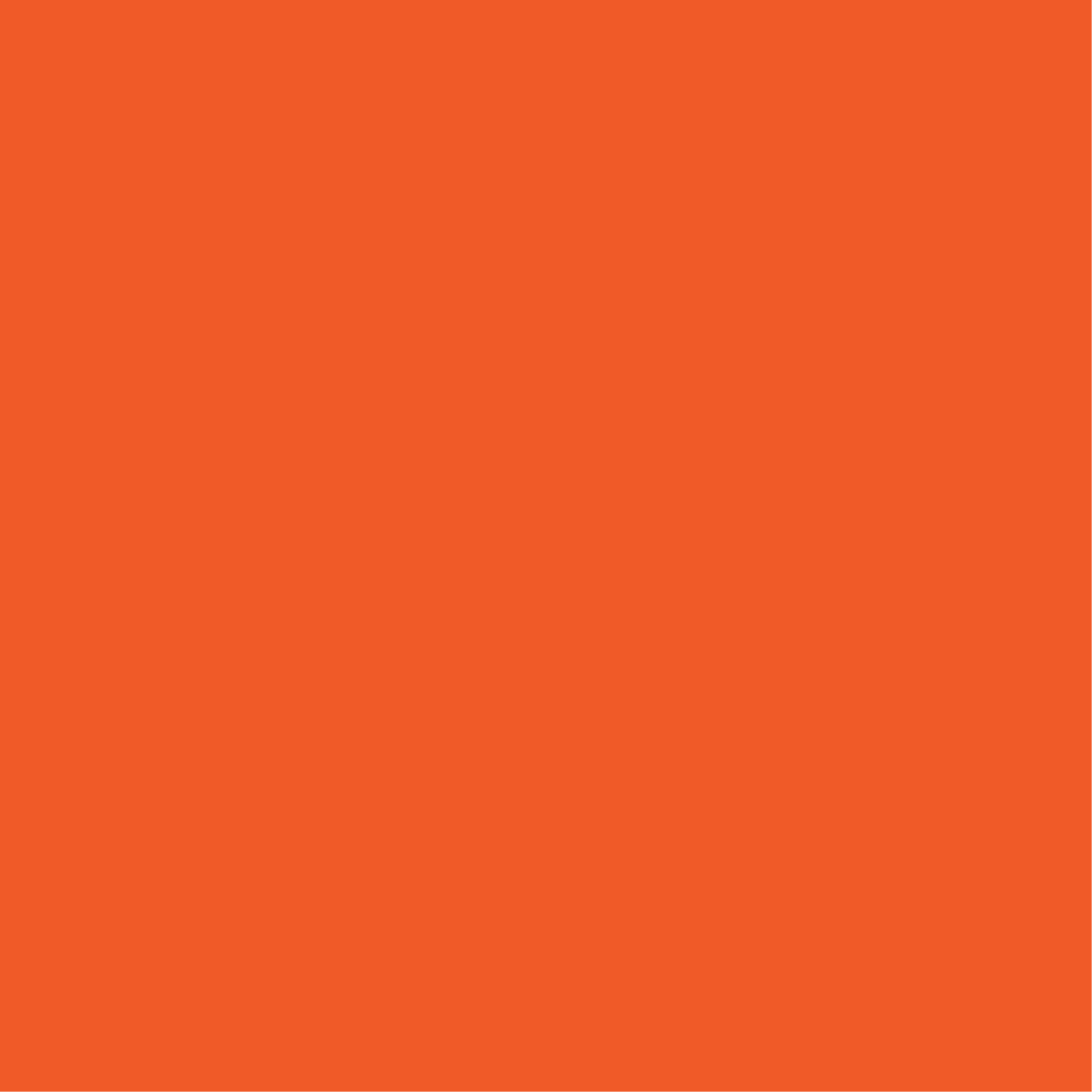

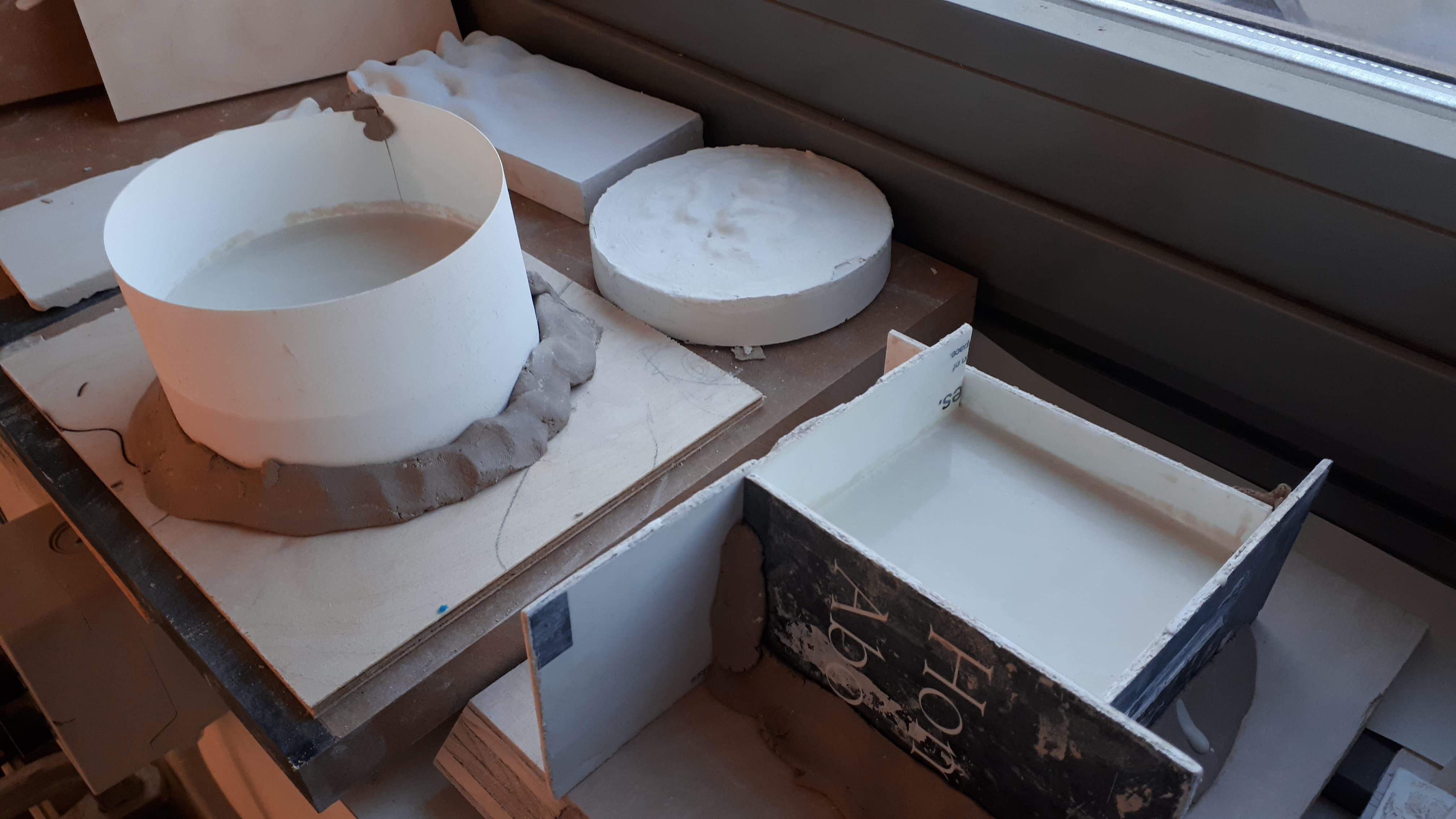
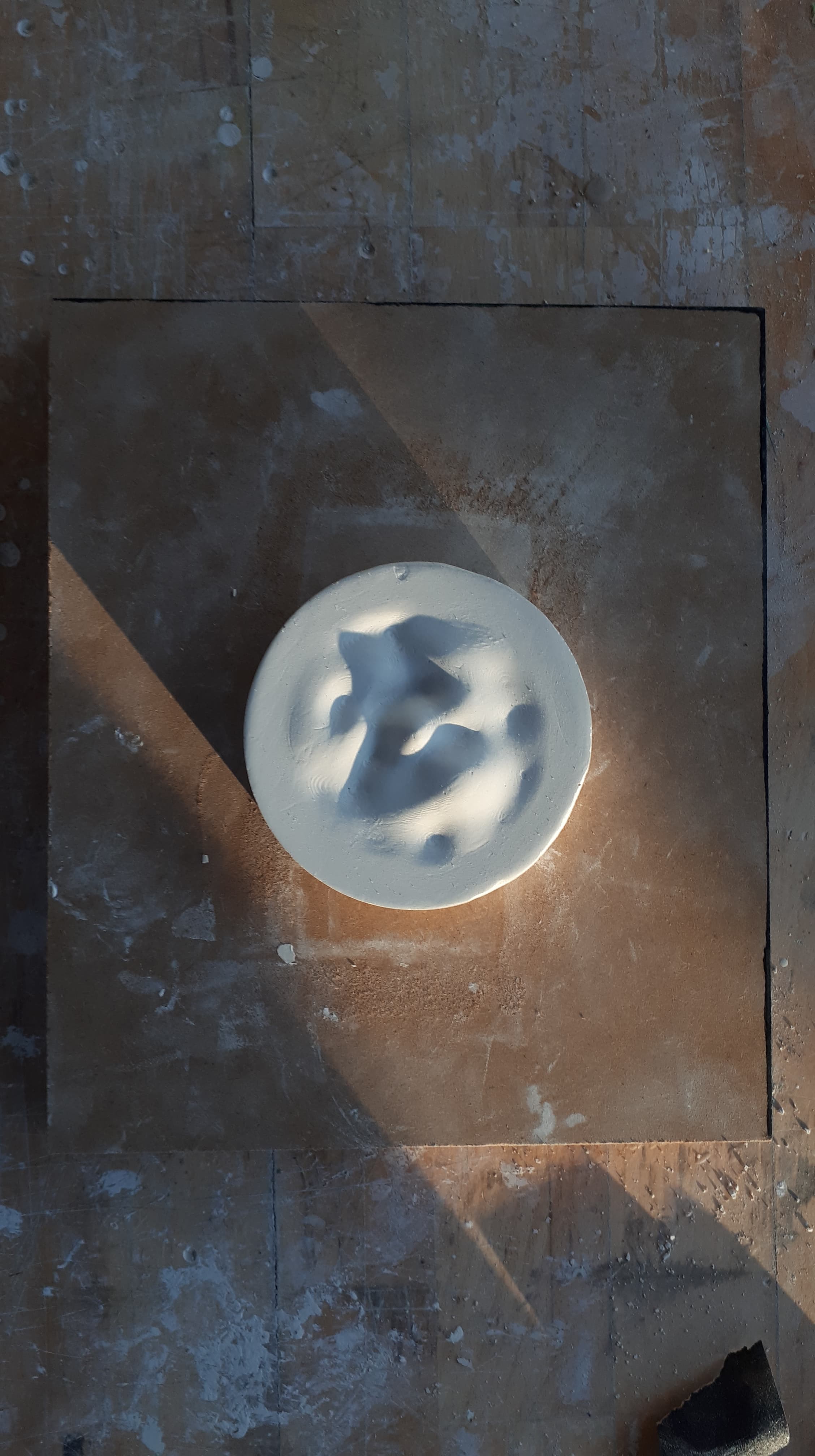
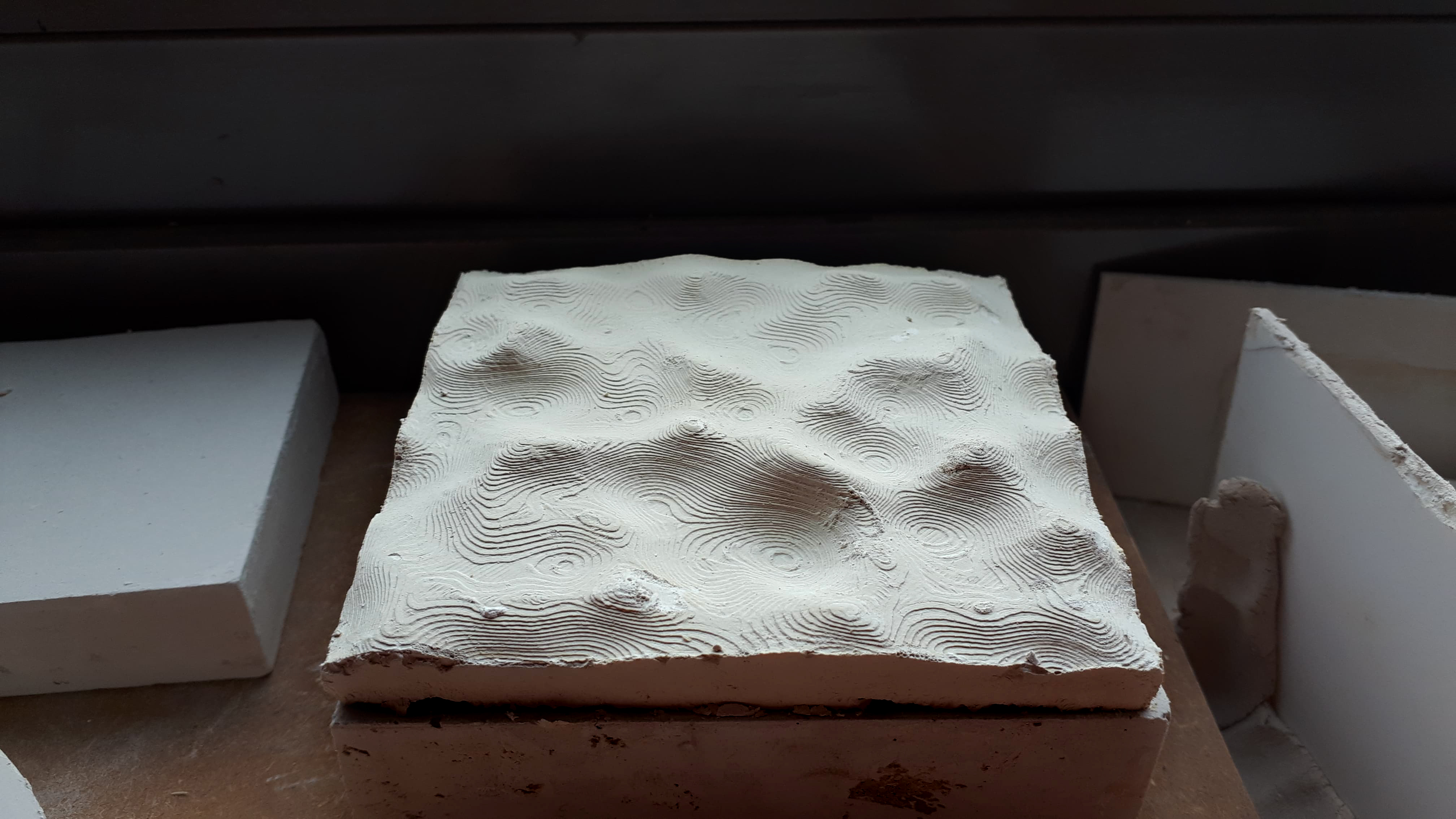
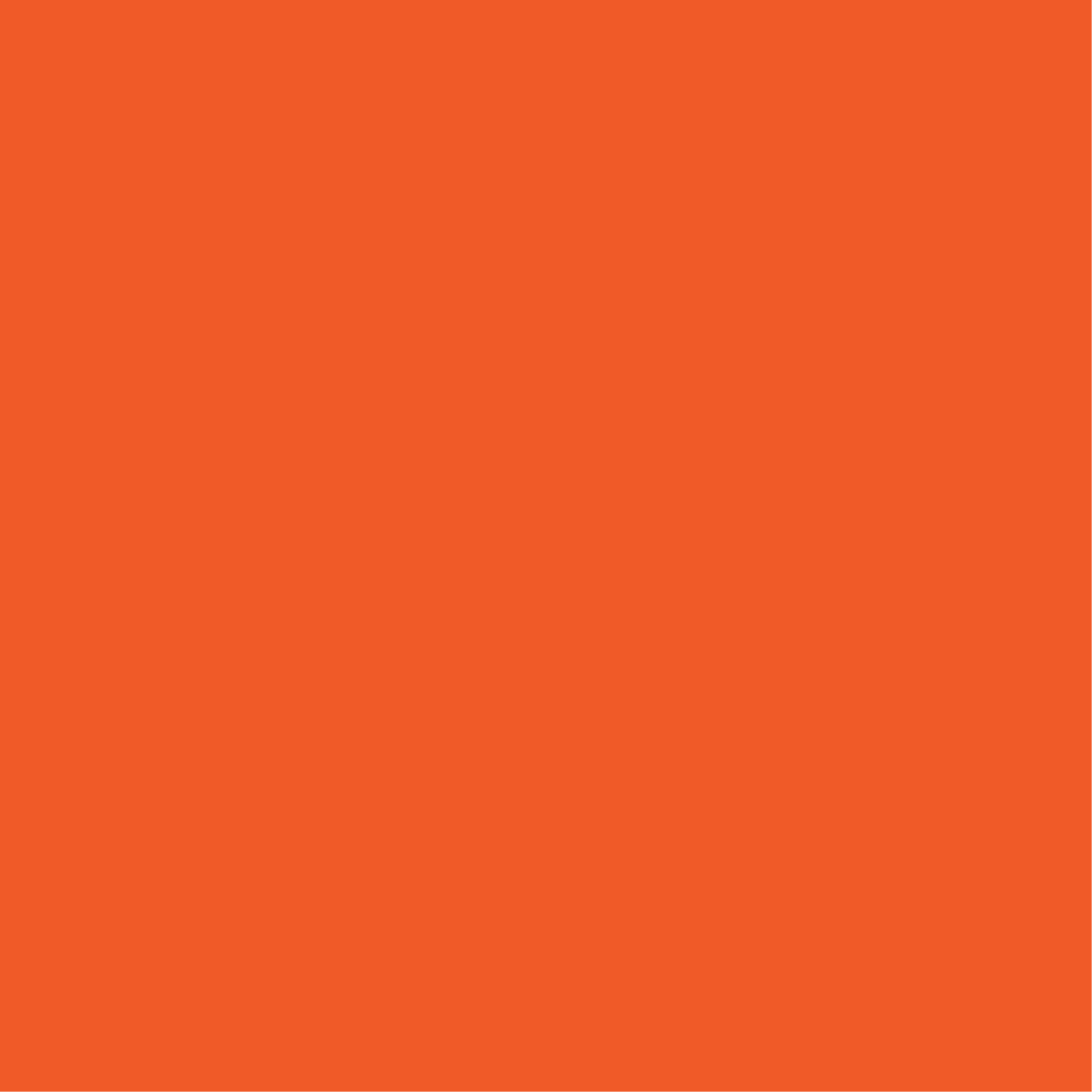
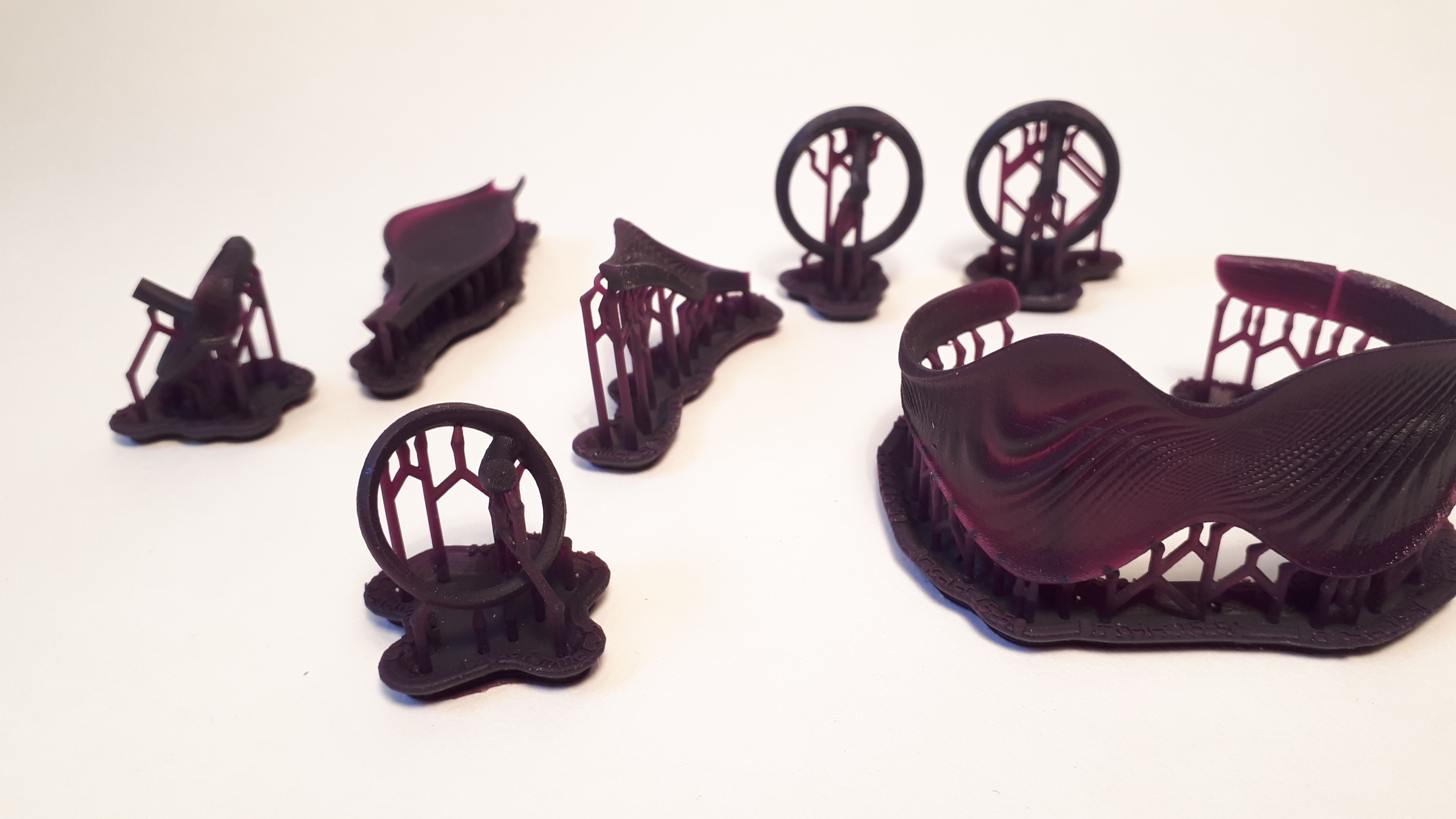
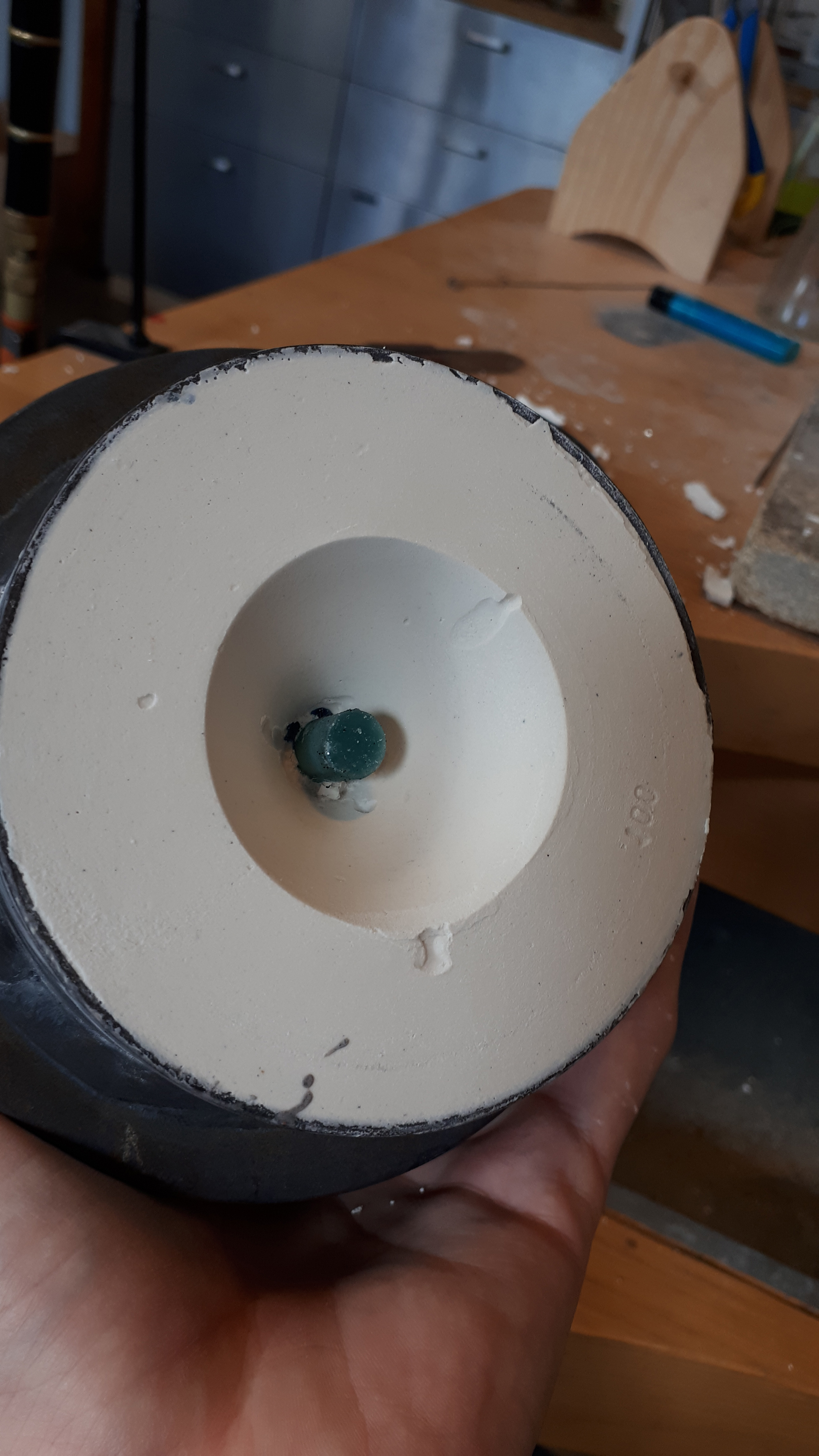

The final pieces convey the original idea of the fluid state materials go through when poured into the mold; this dimension is enhanced by the difference in scales and patterns that can be observed between ceramic and metal items - but also between items of a same material, since all of them sport unique patterns.
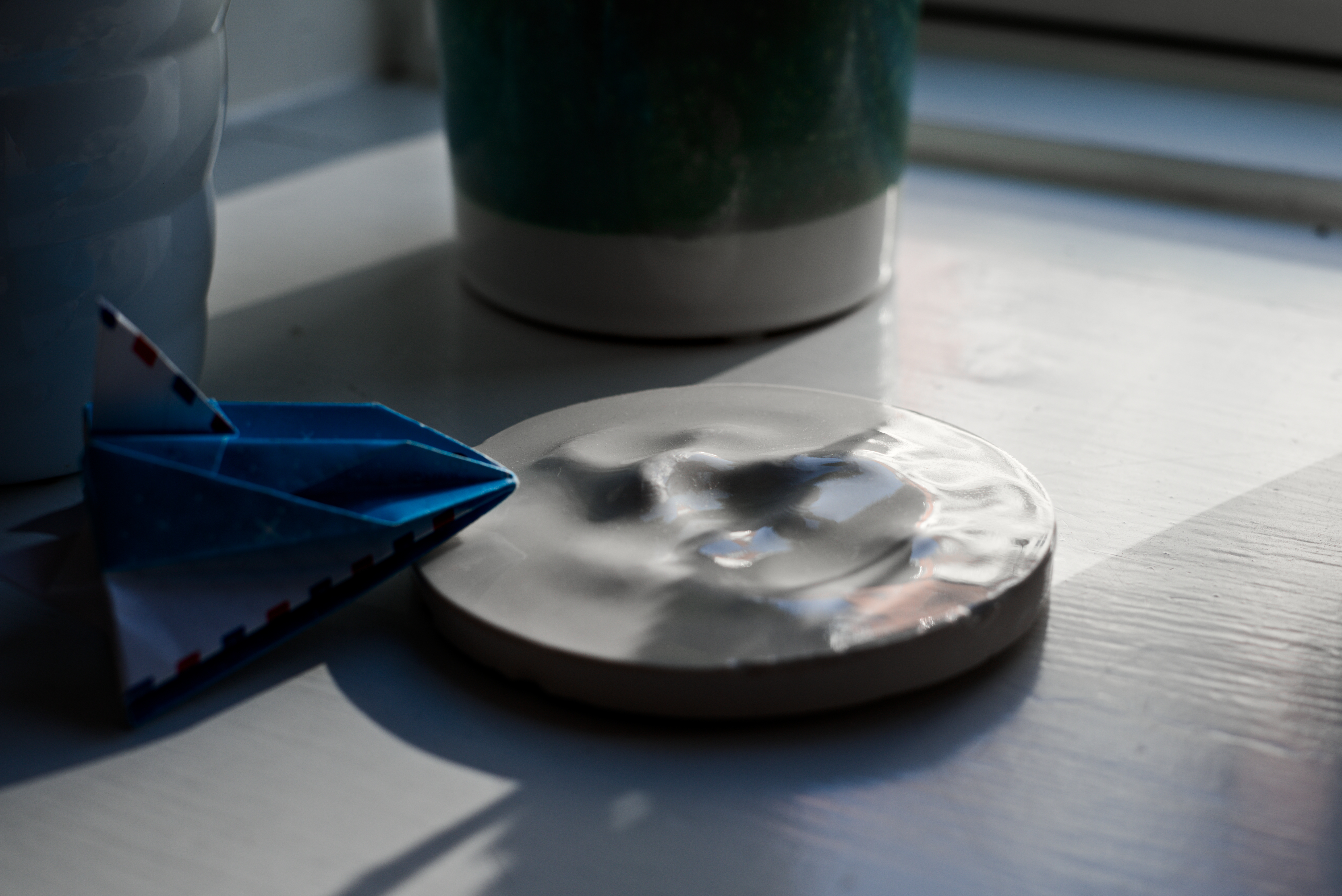
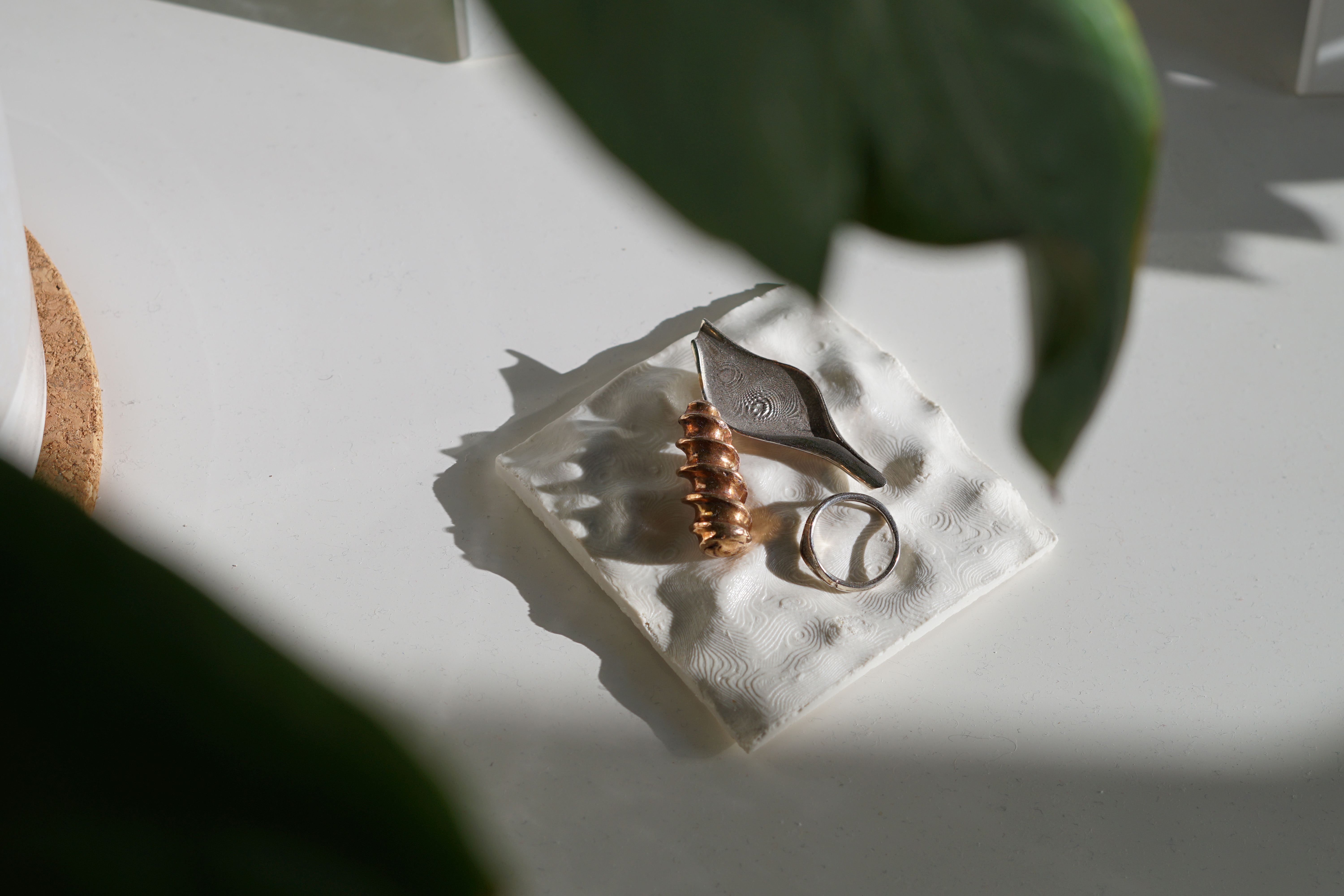
State of affairs
This initial collection led to the creation of a second range, created in collaboration with fashion designer Ninon Lê Van, where the metal undulations enhance, while contrasting them, the floral patterns of the garments. Have a look at our collaboration here.